We have served our customers with a wide range of casting products in different materials.
Casting process
Sand casting
Rapid casting
Permanent mold casting
Lost wax casting
Lost foam casting
Investment casting
Die Casting
Centrifugal casting
Shell mold casting
Vacuum casting
Materials
Aluminum
Stainless steel
Steel
Brass, copper zinc alloys
Zinc, Zinc alloys
With our experience in casting and we consult our clients to choose the most cost effective process under different points of view:
Required quality of the casting surface
Required dimensional accuracy of the casting
Quantity of casting products
Casting product material
Type of pattern and core box equipment needed
Cost of making the mold(s)
Influeuce on the design of the casting with selected process.
Each casting process has its advantages and disadvantages depended on the products needs:
Sand Casting
Sand casting is one of the most popular and simplest types of casting, and has been used for centuries. Sand casting allows for smaller batches than permanent mold casting and at a very reasonable cost.
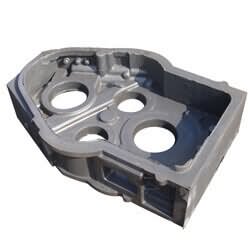
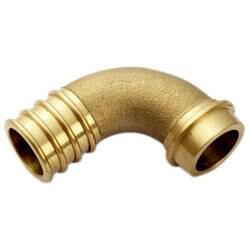
Shell Mold Casting
Our foundry in Zhejiang does shell mold casting for steel and aluminum. The resin sand mold enables complex geometries to be cast. We typically manufacture medium size parts require high accuracy such as gear housings, heat exchanger, connecting rods, and lever arms.
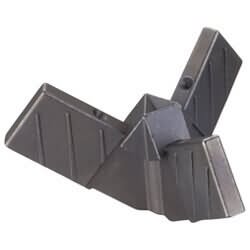
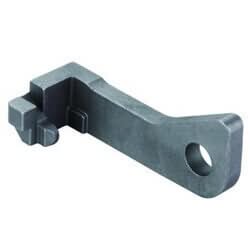
Lost Form Casting
Lost form casting offers similar benefits as lost wax casting, but avoiding complex process of making wax shell. It is relatively simple to make mold and allows recycling of sand. It is consisted of three stages:
White Mold Stage: Mold Foam into shape
Yellow Mold Stage: Coating the Mold
Black Mold Stage: Pour Liquid Metal, which takes place of the foam.
Our facility has excellent capacities to do Lost Foam Casting. In addition, we work closely with leading research institute in China to obtain chemicals used in the process and reduce pollution.
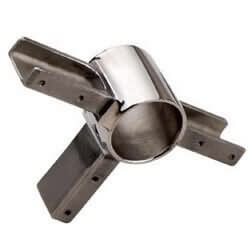
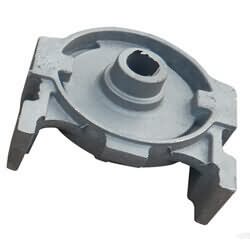
Vacuum Casting
Vacuum casting uses a plastic film to cover sand surface and uses vacuum to shape sand. It produces casting parts with better surface and dimensional accuracy. It is a greener method than traditional casting. Our factory in Jiangsu China can cast steel or s.g. iron, from weight 10Kg to 3000kg. Please see the pictures below for samples of products.
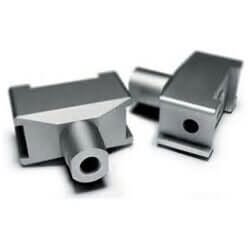
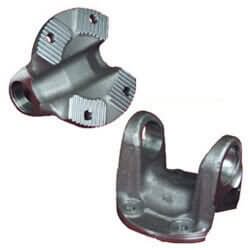
Centrifugal casting
In this process molten metal is poured in the mold and allowed to solidify while the mold is rotating. Metal is poured into the center of the mold at its axis of rotation. Due to centrifugal force the liquid metal is thrown out towards the periphery.
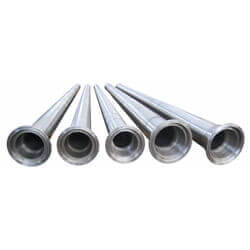
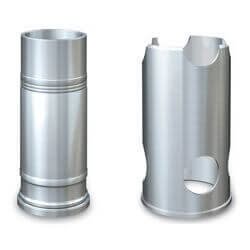
Permanent mold
Permanent mold casting is a metal casting process that employs reusable molds ("permanent molds"), usually made from metal. The most common process uses gravity to fill the mold. However, gas pressure or a vacuum are also used.
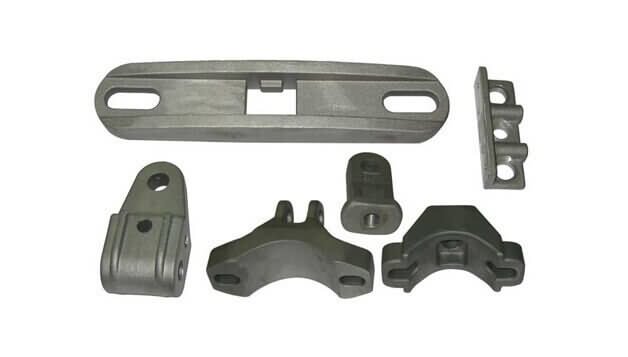
Lost Wax Casting
Lost-wax casting (also called investment casting) is the process by which a duplicated metal sculpture (often silver, gold, brass or bronze) is cast from an original sculpture. Variations of the process include: "lost mold", which recognizes that materials other than wax can be used (such as: tallow, resin, tar and textile) and "waste wax process" (or "waste mold casting"), because the mold is destroyed to remove the cast item.
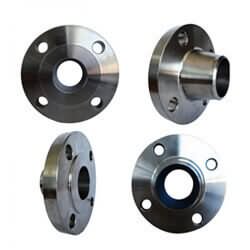
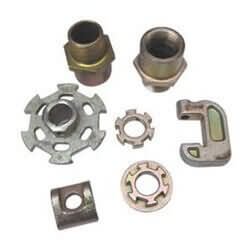
Die Casting
The die casting process forces molten metal under high pressure into mold cavities (which are machined into dies). Most die castings are made from nonferrous metals, specifically zinc, copper, and aluminum-based alloys, but ferrous metal die castings are possible. The die casting method is especially suited for applications where many small to medium-sized parts are needed with good detail, a fine surface quality and dimensional consistency.
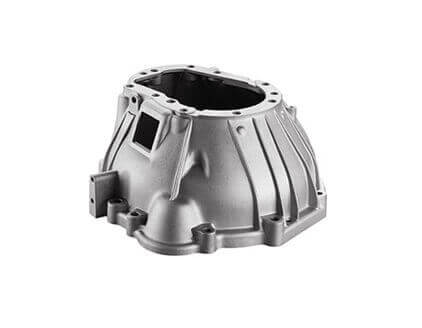
Most of the cast products require machining process after casting. Our customers ask for rough or precise machining. It helps to detect casting defects before shipping. We are familiar with machining properties of various cast steels materials. Typically, we can machine economically for IT6 to IT8 dimensional tolerance levels.
Furthermore, we are offering our customers a one stop solution . For example, after casting and machining the metal products we finish with surface treatment:
Powder Coating
Spray painting
Silk printing
Galvanizing
Polishing
Anodizing