Hot Forging
The hot forging manufacturing process is performed at extreme high temperature (up to 1150 °C for steel, 360 to 520 °C for al-alloys, 700 to 800 °C for cu-alloys). This temperature is necessary in order to avoid strain hardening of the metal during deformation.
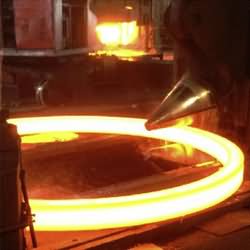
Hot Forging Advantages
Hot forged components possess increased ductility which makes them desirable for many configurations. Also, as a technique hot forging is more flexible than cold forging, since customized parts can be manufactured. The excellent surface quality allows a wide range of finishing work as polishing, coating or painting, tailored to customers’ specific needs.
Hot Forging Disadvantages
Less precise dimensional tolerance is a possible disadvantage of hot forged components compared to the cold forged ones. The cooling process should be also performed under special conditions; otherwise there is a risk of warping. Also, the grain structure of forged metals may vary and there is always a possibility of reactions between the atmosphere and the work piece.
Cold Forging
The cold forging manufacturing process is performed at room temperature. The work piece is squeezed between two dies until it has assumed their shape. To deliver a finished, ready to fit component, the technique includes rolling, drawing, pressing, spinning, extruding and heading.
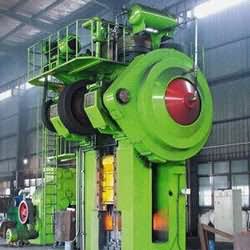
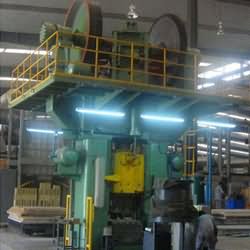
Cold Forging Benefits
Manufacturers may prefer cold over hot forging process; since cold forged parts require very little or no finishing work, which saves cost. The second significant advantage is the material savings achieved through precision shapes. The economic advantages combined with high production rates and long die life are more than enough to convince many manufacturers that cold forging is the best option for them.
Cold Forging Disadvantages
Depending on the manufacturer’s requirements, some of the cold forging characteristics may turn out disadvantages; e.g. only simple shapes in high volumes can be shaped. Therefore, if the customer is searching for a specific customized component, cold forging won’t be the best alternative. A second more significant disadvantage is that cold forged metals are less ductile, which makes them inappropriate for certain configurations. Also, because of the grain structure that gives the material its strength, residual stress may occur.
Our Work:
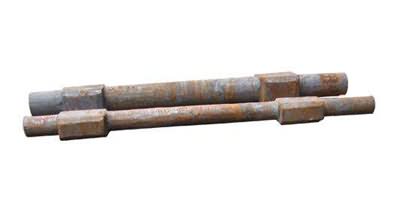
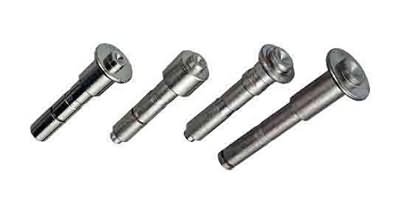