Iron Casting in China
We offer green sand casting, resin sand casting as well as shell mold casting. The company is ISO9001 certified and produce according to international engineering standards.
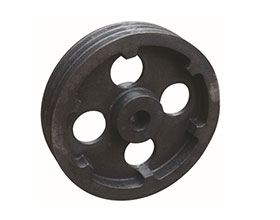
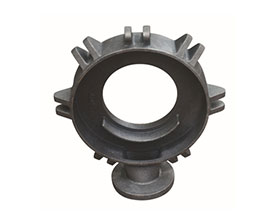
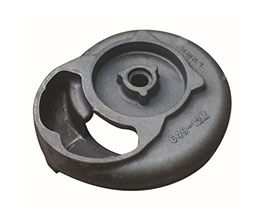
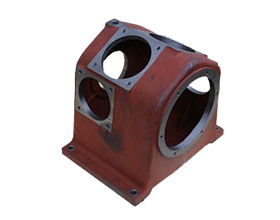

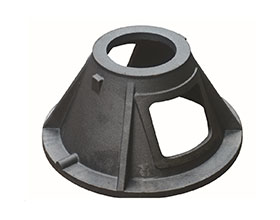
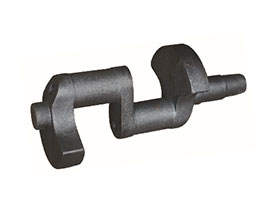
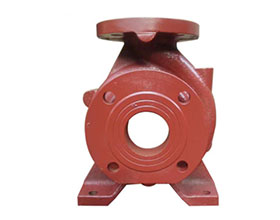
Sand Casting Production Floor:
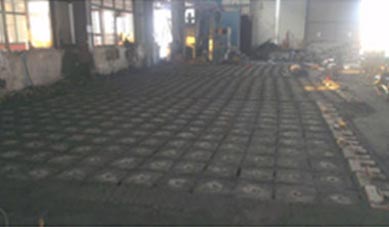

Shell Mold Casting:
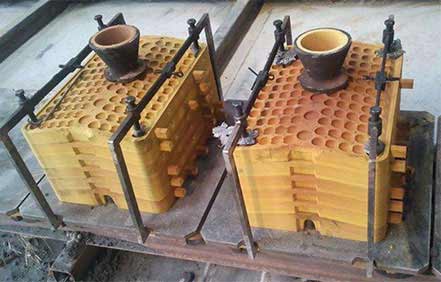
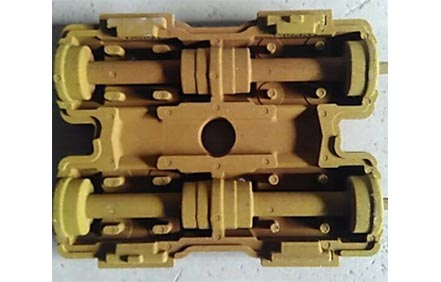
Material Choices:
Pearlitic malleable iron ASTM A220: 40010 (DIN GTS-45),50005...
Ductile cast iron ASTM A536: 60-40-18 (DIN GGG40), 65-45-12, 70-50-05...
Grey cast iron ASTM A48: Class No.60 (DIN GG40) to No.400 ...
Gray Iron:
Gray iron or grey iron is an alloy of carbon, silicon, and iron, containing from 1.7 to 4.5% C and 1 to 3% Si. It is relatively easy and inexpensive to make. Gray iron has a lower tensile strength and lower ductility.
It fails more easily, and its mode of failure will be sudden fracture (it will not bend). Gray iron is often used for housings where tensile strength is non-critical, such as engine blocks, pump housings, valve bodies, decorative castings and electrical boxes.
Pearlitic Malleable Iron:
The structure being a metastable carbide in a pearlitic matrix. Through an annealing heat treatment the brittle as cast structure is transformed. Carbon agglomerates into small roughly spherical aggregates of graphite leaving a matric of ferrite or pearlite according to the exact heat treat used.
It is often used for small castings requiring good tensile strength and the ability to flex without breaking (ductility). Electrical fittings, hand tools, pipe fittings, brackets, mining hardware, farm equipment, and machine parts.
Ductile Iron:
also called nodular cast iron, or ductile iron. has a higher "yield strength" than malleable iron, meaning it can bear greater loads.
Green Sand Casting
Advantages of Green Sand Casting:
1. Most ferrous / non-ferrous metals can be used.
2. Low Pattern & Material costs.
3. Almost no limit on size, shape or weight of part.
4. Adaptable to large or small quantities.
5. Used best for light, bench molding for medium-sized castings or for use with production molding machines.
Resin Sand Casting
The chemical bond sand consists of sand and synthetic binders cured thermally or chemically. Allows production of more complex and accurate shape.
Shell Mold Casting
Shell mold casting process offers better surface finish, better dimensional tolerances, and higher throughput due to reduced cycle times. The materials that can be used with this process are cast irons, and aluminum and copper alloys. Typical parts made with this process are connecting rods, gear housings, lever arms etc.
Shell Molding Casting Includes the Following Steps:
1. Sand is pre-coated with a resin that bonds the sand grains together.
2. A tool, or pattern, is coated with the resin coated sand.
3. The coated pattern is heated, curing or hardening the sand. This part of the process bonds the resin and sand creating a hard surface shell that is .5” to 1” thick.
4. The hardened shell mold is stripped from the pattern. This creates one half of the cavity that will be used as the mold. The process is repeated to create the other shell mold half.
5. Two shells are glued together to form the cavity that holds the molten metal.
6. Once the mold is created it is loaded onto the conveyor line and molten metal is poured into it.
7. After the mold goes through a cooling process, the sand shell is stripped from the casting.
8. The sand is recycled and the part is ready for machining or surface finishing.