Investment Casting is also known as Lost Wax Casting is generally used for small castings are made from almost any metal, especially stainless steel. This process generally more expensive per unit than die casting or sand casting but with lower tooling cost. It can produce complicated shapes that would be difficult or impossible by normal manufacturing techniques. Parts made with investment castings often do not require any further machining, because of the close tolerances that can be achieved.
Sodium Silicate Investment Casting
1.The coasting bond brushed on the pattern surface is water glass in this process.
2.Compared with the sand castings, parts made with lost wax casting(water glass) have better surface quality (surface roughness to 12.5 microns) and higher dimensional accuracy.
Silica Sol Investment Casting
1.The coasting bond brushed on the pattern surface is silica sol in this process.
2.Parts made with lost wax casting(silica sol) have the tolerances are 0.1 mm for the first 25 mm (0.005 in for the first inch) and 0.02 mm for the each additional centimeter (0.002 in for each additional inch).
3.A standard surface finish is 1.3 – 4 microns (50 –125 μm). Compared with the water glass process, parts made with lost wax casting(silica sol) have excellent surface finish and higher dimensional accuracy.
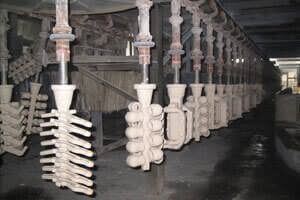
The Process of Investment Casting:
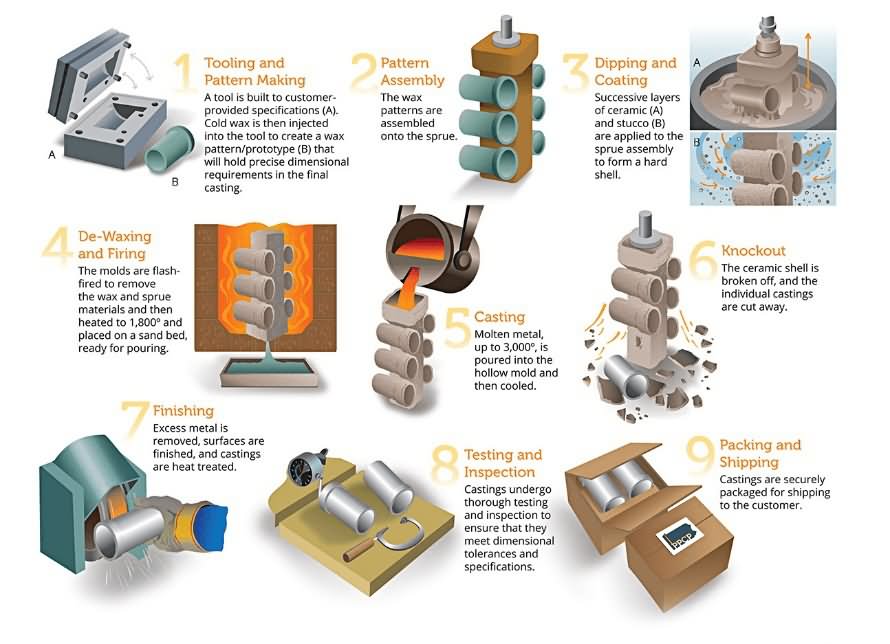
The Advantages of Lost Wax Casting:
Excellent surface finish.
High dimensional accuracy.
Extremely intricate parts are cast able.
Almost any metal can be cast.
No flash or parting lines.
Some samples of our investment casting production:
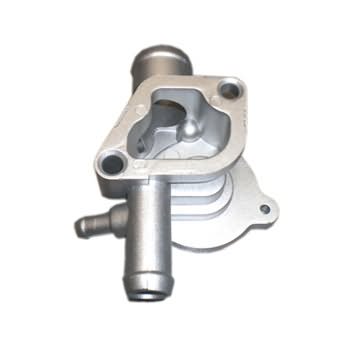
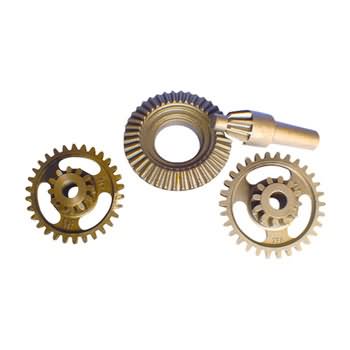
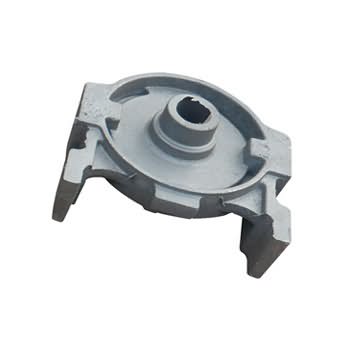